The challenge of achieving tunnel vision during underwater ROV inspections
At EIVA, we are seeing more and more applications of NaviSuite Mobula, a topside control and inspection software solution for ROV (Remotely Operated Vehicle) operations. Our customers often carry out surveys in hard-to-reach places that require sophisticated software for their customised ROVs, because a standard ROV – with video feed alone – rarely meets the demands of complex operations.
Tunnel inspections are one of the more challenging types of underwater survey, and for several reasons: the length and shape of the tunnel, murky water, and zero visibility. Each factor presents a unique challenge to the ROV, which often puts demands and restrictions on the hardware and software. In response to this, ROV operators are turning to customisable setups with versatile software to overcome difficult conditions.
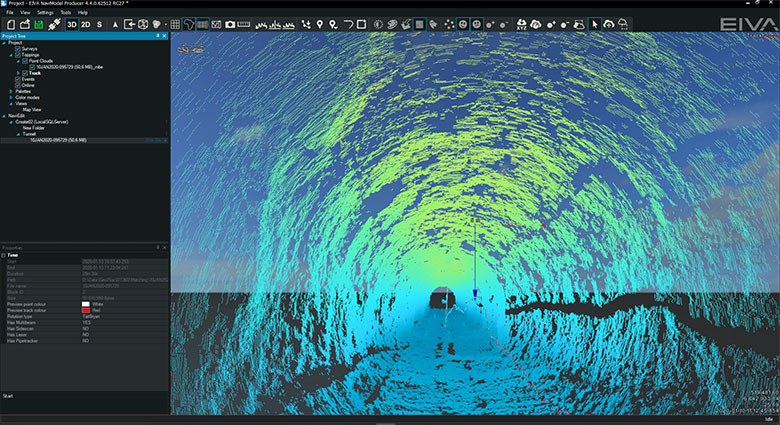
An ROV inspection operation in a flooded tunnel which is only accessible from the water side - image courtesy of GeoPluss and NTI
Who and why carry out underwater tunnel inspections?
Water supply companies and governments who are responsible for dams, reservoirs and hydroelectric plants, or any large volume of water, often carry out inspections as a pre-emptive safety measure to identify any potential issues. Additionally, mining operations and companies involved with large drainage channels require technology to perform underwater inspections in tunnels, shafts and caverns.
Alongside the monitoring of structural integrity, the search for leaks and voids, volumetric assessments of debris and sediment, as well as repair assessments are conducted during an inspection. Dewatering of tunnels is expensive, and potentially causes stress to the structure of the tunnel itself, which is why many favour the use of an ROV. However, the use of an ROV can also be expensive due to the unique conditions and challenges involved.
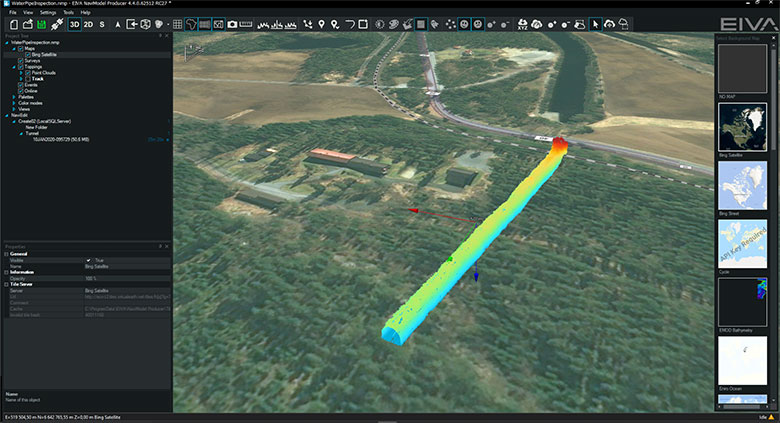
An aerial view of a water pipe inspection modelled in NaviModel, which is included in + Processing variants of NaviSuite Mobula and includes high-performance capabilities for the creation of digital terrain models in 2D, 3D and 4D for data analysis and manipulation – video courtesy of GeoPluss and NTI
Solving the obstacles an ROV faces when inspecting an underwater tunnel
Operational space; the size and shape of the tunnel can limit access and restrict the size of the ROV. The use of small ROVs with advanced manoeuvring capabilities can be the answer to this problem. A small ROV with a minimal footprint, six degrees of freedom, that is backed up by ROV software with advanced steering control features, would diminish most restrictions put on it by operational space.
The positioning of the ROV is limited due the lack of GPS/GNSS, and difficulty with acoustic and USBL (Ultra-Short BaseLine) positioning. Both the price and size of a high-end INS (Inertial Navigation System) solution hinders its use in the reality of tunnel inspections where size and payload capacity are limited – even though an INS would provide perfect positioning accuracy. One solution involves a cable counter and clever software. By feeding the GPS coordinates at the beginning and end of the tunnel, the length of tunnel, the length of umbilical tether, the time taken, and the speed of the ROV, all into NaviEdit, the software can then process and calculate the position of the ROV. NaviEdit enables the import of raw sensor data such as laser and sonar for the purpose of editing.
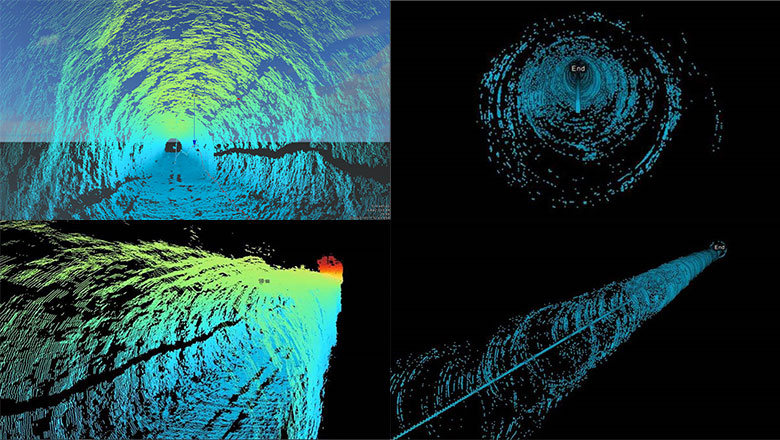
The tunnel visualisation on the left was a result of positioning based on recorded cable length using a multi-beam sonar, whereas on the right, the data was collected without a cable indicator by simply interpolating between start and end position using a single beam profiling sonar – images courtesy of GeoPluss and NTI (left) and Bay Dynamics NZ (right)
When visibility is poor, streaming real-time video is not an option, which eliminates the possibility of camera-based solutions. Sonar is one alternative; however, the addition of sonar creates demands on the ROV’s payload capacity and its software regarding sensor integration, specifically its ability to process and model the environment in real-time. Accurate 3D modelling allows the operator to steer the ROV safely and efficiently. Furthermore, specialised 360° sonar is required to map the tunnel and minimise the number of scanning runs while maximising the quality of data collected. The cheapest scanning sonars can create patchy data and often require several runs to compensate – which is not always desirable where navigation is challenging, and the budget is as tight as the operating space. The best sonars on the market are accurate enough to pinpoint cracks in the structure of tunnel walls yet come with a high price tag. The result being that the type of sonar required will depend on the purpose of inspection, from sediment build-up to structural checks.
Tethered ROVs are often fed with power while transferring data to the operator. Long tunnels can demand kilometres of umbilical tether, which require a large winch, a large crew, and sometimes a forklift. Battery powered ROVs are a cheaper alternative in these circumstances. On the one hand, battery power allows for a thinner, lighter fibre-optic cable, which reduces cable thickness and drag, and the size of the winch needed. On the other hand, the length of the tunnel restricts the range of the ROV. When tunnel access is limited to one-point, additional power is needed to reach the end of the inspection area and return, which suggests a battery pack fit for purpose as the ideal solution.
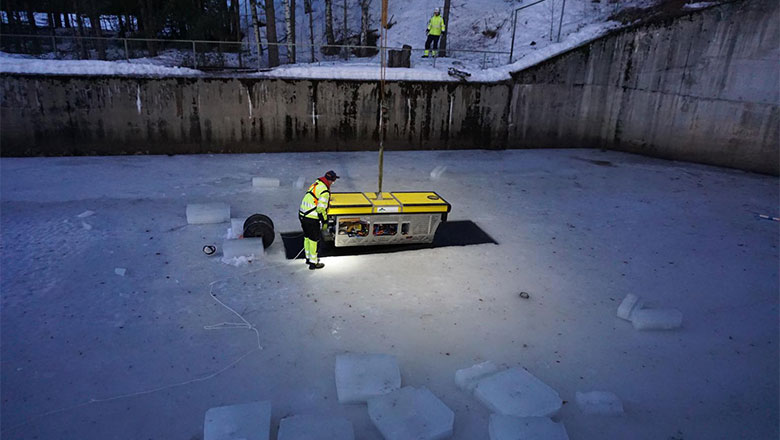
Breaking the ice. An ROV powered by onboard batteries with a thin fibre-optic cable to transfer data – Picture courtesy of GeoPluss and NTI
The short story, tunnel inspections with an ROV can be complex, time consuming, labour intensive and expensive. To reduce costs, a unique setup with a balance of hardware and software is required. One that has the potential to maximise operational efficiency and help cope with the demand put on the ROV by the challenging environment.
Our recommended setup for affordable ROV tunnel inspections
During a tunnel inspection where visibility is poor, the ROV should ideally be fitted with a sonar to provide 360° visualisation and mapping. The DT360 from Imagenex would be well suited to the task because of its ability to scan 360° horizontally with a relatively narrow beam width, as well as the BlueView T2250-360 from Teledyne. There are not many scanning sonars on the market with those capabilities, and these middle-market priced sonar both minimise the number of scanning runs required while maximising the quality of data collection. This makes them suitable for most types of tunnel inspections, from pinpointing small cracks to complete sediment blockages. The BlueROV2 from Blue Robotics has a small footprint, is light, manoeuvrable, affordable, integrates with sonar, and comes with excess payload capacity for extra batteries when built with a custom frame design. It is the cheaper alternative to existing ROV solutions on the market. The thinner, data-only tether will reduce the size of winch and crew needed for an operation; however, the lack of topside power will limit its range and run time.
Our recommended software setup for efficient ROV tunnel inspections
NaviSuite Mobula is a topside software solution for processing raw sensor data and modelling live sonar imagery and mosaic during zero-visibility conditions. Alongside the standard steering control seen in most ROV software, NaviSuite Mobula has assisted steering with lock depth and lock headings and provides a single interface with a multitude of features. Real-time data interpretation can be displayed in customisable and multiple views, which enables precise ROV control in difficult conditions to allow for thorough data collection and safer navigation. Furthermore, NaviSuite Mobula can manage eventing and registration of objects, to create more routine inspections that require little operator input. With + Processing variants, all survey data can be recorded and delivered via NaviModel for post operation evaluation, which means less on-site decision making, the chance for a second opinion, and deliverable data to an end client.
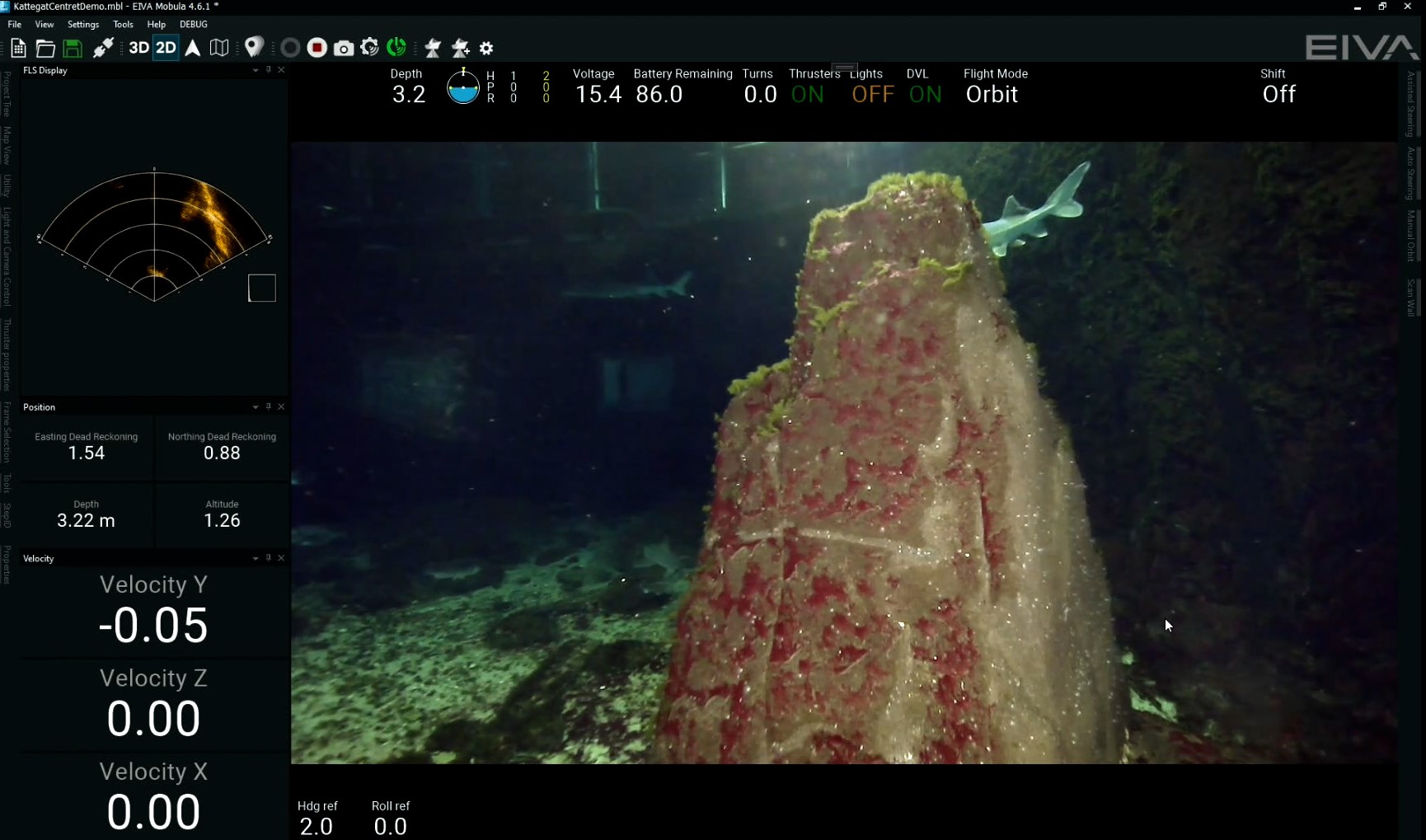
NaviSuite Mobula in assisted steering mode displaying live data, an FLS wedge view and video feed
NaviSuite Mobula is compatible with a wide array of sonars and can post-process sonar and video feed all in one data set. The software bundle comes with enhanced asset integrity management, which improves the capacity to run effectively and accurately. Models and datasets from previous inspections can be uploaded. After the first 3D model is overlaid, it becomes 4D with the inclusion of time as the fourth dimension, which in turn makes each inspection easier and more efficient as previous areas of interest are easily identifiable and located.
Currently, NaviSuite Mobula ROV control and inspection software is integrated with Blue Robotics BlueROV2 and VideoRay Defender platforms – however given a little coding, it can be configured for any ROV.
If you believe this combination of hardware and software can benefit your tunnel inspection operation, or you’re struggling with a unique challenge, please get in touch and we’ll do our best to find a solution that meets your needs.